Driving the Future of Drainage - Business in Focus Magazine - Nov 2015
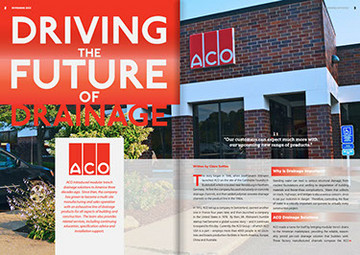
ACO introduced modular trench drainage solutions to America three decades ago. Since then, the company has grown to become a multi-site manufacturing and sales operation with an exhaustive line of drainage products for all aspects of building and construction. The team also provides related services, including continuing education, specification advice and installation support.
The story began in 1946, when Josef-Severin Ahlmann launched ACO on the site of the Carlshütte Foundry in Budelsdorf, which is located near Rendsburg in Northern Germany. At first the company focused exclusively on concrete drainage channels, and then added polymer concrete drainage channels to the product line in the 1960s.
In 1972, ACO set up a company in Switzerland, opened another one in France four years later, and then launched a company in the United States in 1978. By then, Mr. Ahlmann’s humble startup had become a global success story – and it continues to expand to this day. Currently, the ACO Group – of which ACO USA is a part – employs more than 4000 people in 40 countries and boasts production facilities in North America, Europe, China and Australia.
Why is Drainage Important?
Standing water can lead to serious structural damage, from cracked foundations and settling to degradation of building materials and freeze-thaw complications. Water that collects on roads, highways, and bridges is also a serious concern, since it can put motorists in danger. Therefore, controlling the flow of water is a critically important component to virtually every construction project.
ACO Drainage Solutions
ACO made a name for itself by bringing modular trench drains to the American marketplace, providing the reliable, reasonably priced pre-cast drainage solution that builders seek. These factory manufactured channels compose the ACO Drain product line and come in meter or half-meter lengths, making transporting to the job site and on-site handling a snap. Once onsite, channels are aligned into versatile configurations via male/female interconnecting ends to form a continuous sloped run. With up to 40 interconnecting channel sizes available in one system, modular sloped trenches can be as long as 125 feet. Neutral channels with no slope can be inserted within that run to create an even longer system.
Modular trench drains are more affordable and save installation time and effort. “Cost comparisons have shown modular trench drains to have lower total installed costs when labor, excavation, pipework, grading etc., are taken into account,” explains Jaclyn Revis, Marketing Services Manager for ACO USA. “On average, pre-cast modular trench drains cost about 10 percent less to install and maintain than catch basin systems, and 20 percent less than cast-in-place trench drain systems.” At just four inches wide, the narrow width of modular channels helps keep costs down. “These narrower widths use smaller grates, significantly reducing overall project costs,” Mrs. Revis explains. “Wider systems are available if required by hydraulics or application.”
Armed with a dedicated research and development department, ACO designs and produces a number of innovative, market leading drainage systems that meet the drainage needs of many industries and specific applications. ACO Sport – the company’s sport field and stadium drainage system – has been used at Olympic venues since 1972. This product line earned special recognition during the 2014 World Cup games in Brazil, when it kept the stadium in working condition during a brutal downpour. While the surrounding streets flooded, ACO’s trench drainage system kept the soccer field relatively dry, allowing the United States and Germany to play a match that would have otherwise been canceled.
ACO Environment helps control pollution with liquid and solid separators and spill containment systems that are manufactured from corrosion-resistant materials. Specializing in custom drainage solutions, ACO Aquaduct provides products made from FRP (fiberglass reinforced plastic), stainless steel and other materials. ACO Utility Duct supplies surface ducting systems that are designed to protect cables and pipes against external influences. ACO Wildlife supplies tunnels and fence systems that help wildlife cross dangerous roads safely.
One of ACO’s newest product lines, ACO Stainless, includes stainless steel drainage solutions, primarily used for building drainage or commercial kitchen applications where the strength and cleanability of stainless steel is most important. ACO’s philosophy of HygieneFirst represents the team’s commitment to delivering products that provide ultimate hygienic performance. These products are designed to effectively and safely drain away and handle process water and reduce the risk of food contamination.
ACO also offers solutions for residential applications in both exterior landscape applications as well as interior bathroom drainage solutions. ACO Self is a line of residential trench drain products designed for the landscaper, builder, or do-it-yourself enthusiast. The QuARTz ACO ShowerDrain products are designer bathroom products that include point and linear shower drains with a variety of grate designs, finishes, lengths and accessories. QuARTz products are often used in hospitals, hotels, resorts and residential homes.
ACO StormBrixx is a unique and patented plastic geocellular stormwater management system. Designed for surface water infiltration and storage, its versatility allows it to be used in applications across all construction environments as a standalone solution or as part of an integrated sustainable urban drainage scheme. ACO Infrastructure includes a range of surface drainage products specifically engineered for highways, urban roads, bridges, docks and airports. This range includes Qmax, a high-capacity slot drainage system that allows an unbroken reinforced concrete slab to be cast around – and through – the inlets for a stronger surround.
Developed to satisfy the demand for an economic, high-capacity drainage system for large catchment areas, Qmax is available in five different sizes. Ideal for racetracks, Qmax is used at some of North America’s top racing venues. For example, the Circuit of the Americas Formula 1 Racing Track in Austin, Texas installed 7000 meters of the product. Mexico’s brand new Formula 1 track – slated to open with the Mexico Formula 1 Grand Prix race on November 1st – has also installed over four miles of drainage systems, including Qmax.
The product has earned national recognition for its creative approach and effective results. In 2012, the Most Innovative Products (MIP) Award Program named Qmax the Most Innovative Product in the Expert’s Choice – General Tools & Equipment category.
Preparing for the Future
ACO’s products have become so popular that the company has recently opened a new manufacturing facility to meet the demands of the United States’ northeastern market. The company’s original factory, located in Chardon, Ohio, was simply unable to accommodate the growing production needs, so a site 16 miles away in Mentor, Ohio was selected that could handle the company’s expanding needs. Production capacity will increase by 35%.
Stocked with the latest, most advanced technology, the new Ohio facility will bring the company’s northeast operations up to speed with other ACO locations. The move will also help grow ACO’s presence in the United States by solidifying the company’s position as the market leader and allowing the team to deliver better quality and service.
Moving forward, ACO will continue to focus on growth, both in sales and in profit. “To achieve these goals, we must continuously improve our product offering through innovations and new product development,” says Vaclav Tikalsky, President of ACO USA. “The company will also need to keep a close eye on its internal processes,” he adds.
ACO will also maintain a strong focus on its people, the backbone of the business. “The company’s success is based on its employees and strong international network of the ACO Group,” Mr. Tikalsky states. “ACO wants to be a good employer, further developing the family culture where people will like their work and enjoy the new facilities which we have built in recent years.”
Mr. Tikalsky credits customers for “asking for the right solutions” and emphasizes how important it is to pay attention to their needs. “ACO will continue to closely listen to their needs,” he says.
The company’s focus on innovative designs, employees, and customer satisfaction has paid off. “The strategies we have in place have proven effective,” Mr. Tikalsky points out. “The company is growing and expanding. Of course, we do have to face some ups and downs like other companies, but overall, we are pleased with our direction.”
The groundwork is laid for ACO to continue to be the single solution for all of its customers’ drainage needs. “Our customers can expect much more with [our] upcoming new range of products,” Mr. Tikalsky shares. “We are bringing awareness to the complete ‘system chain’ for both surface water management as well as building drainage. Our customers will be able to get the right products for situations when they need to ‘collect, clean, hold and release’ the water, from one single source.”
Other Articles You May Like:
ACO Celebrates Grand Opening of New Facility
Optimizing Hygienic Performance with Drainage Design - Part I
Optimizing Hygienic Performance with Drainage Design - Part II
Hygienic Drain Designs, sanitizers and drain management